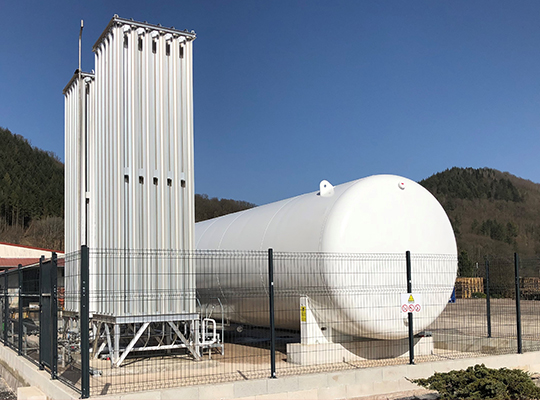
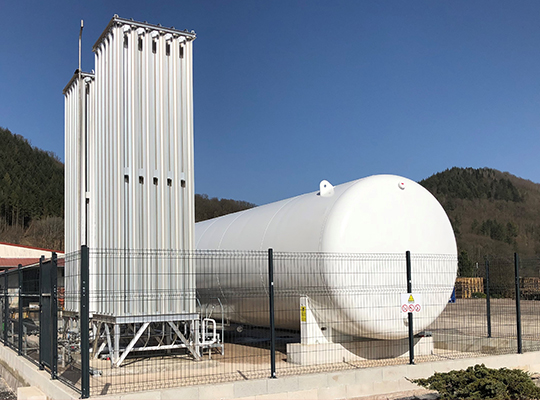
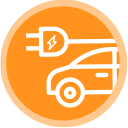
La mise en service d’une installation de regazéification montre que le GNL peut compléter l’offre multi-énergies de TMF.
Après une première réalisation en 2014, TMF vient de construire une nouvelle unité de regazéification de GNL (gaz naturel liquéfié). Elle fonctionne depuis le 2 février sur le site Knauf Industrie de Sainte-Marie-en-Chanois (Haute-Saône). Thomas BONNAVAUD, responsable Nouveaux Marchés / Produits à la direction Grands Comptes Marchés Industriels, et Paul-Hubert FRANÇOIS, directeur Grands Comptes Marchés Industriels (direction Commerce Général), présentent ce projet.
TMF a récemment mis en service une installation de regazéification de GNL sur un site appartenant à Knauf Industrie. Quelle est l’origine du projet ?
Thomas BONNAVAUD : Knauf Industrie, qui fabrique des pièces en polystyrène expansé pour le secteur de l’automobile, possède cinq usines en France. Trois d’entre elles fonctionnent encore au fioul lourd et sont clientes de la direction GCMI (Grands Comptes Marchés Industriels) depuis des dizaines d’années. Le site de Sainte-Marie-en-Chanois (Haute-Saône) en fait partie. Il est équipé d’une vieillie chaudière qui ne permet plus de respecter les valeurs limites d’émissions réglementaires. Le client a donc réfléchi à un changement de combustible et opté pour le GNL (Gaz Naturel Liquéfié).
Paul-Hubert FRANÇOIS : Compte tenu de la distance importante séparant l’usine de Sainte-Marie-en-Chanois du réseau de gaz naturel, Knauf Industrie n’avait d’autre choix qu’une énergie stockable : GNL, GPL (Gaz de Pétrole Liquéfié), biomasse liquide ou solide. Le GNL s’est imposé sur la base de critères technico-économiques mais aussi environnementaux. Utilisé comme combustible, il permet en effet de réduire les émissions de soufre et de particules fines de l’ordre de 99 %, et d’oxyde d’azote jusqu’à 85 %. Le gain est donc très significatif. Outre les polluants atmosphériques, le bénéfice se situe au niveau des émissions de gaz à effet de serre, avec un écart de l’ordre de 20 % par rapport au fioul lourd.

Comment TMF a-t-il gagné la confiance du client ?
T. B. : Les attentes de Knauf Industries portaient principalement sur la fiabilité de l’installation de regazéification du GNL, la garantie de l’approvisionnement et la rapidité du retour sur investissement. Trois entreprises ont été consultées dans le cadre d’un appel d’offres privé. La relation que nous entretenons de longue date avec le client, qui repose sur la confiance et la qualité de service, a sans doute joué en notre faveur. Mais l’essentiel réside dans l’offre que nous avons proposée : à la fois sa qualité technique et sa compétitivité.
P.-H. F. : Ce succès est le résultat d’un très beau travail d’équipe. Tout d’abord au sein du Commerce Général, grâce à l’appui des départements STLQ (Support Technique – Logistique Qualité) pour la construction de l’installation de regazéification et RPO (Ressources – Prix – Opérations) pour la fourniture du combustible. Plus largement, toutes les entités de TMF impliquées dans le développement du GNL se sont mobilisées. Je pense plus particulièrement aux directions MNE (Mobilités et Nouvelles Energies) et SLF (Supply et Logistique France). La réussite collective est d’autant plus remarquable que le projet a pu être concrétisé en moins d’une année et malgré deux confinements !
Quel parcours suit le GNL entre son arrivée à Zeebruges et son utilisation dans le process industriel ?
T. B. : Le produit est transporté par un camion cryogénique dont la capacité est de l’ordre de 20 tonnes. Il faut rappeler que le GNL est refroidi à -163 °C, état dans lequel il prend 600 fois moins de place que le gaz à température ambiante. Nous tablons sur environ une livraison par semaine, exception faite de la période estivale, ce qui correspond à un approvisionnement annuel estimé autour de 800 tonnes. Une fois déchargé sur le site de Knauf Industrie, le GNL est stocké dans une cuve horizontale d’une capacité de 33 tonnes. La regazéification se déroule à l’aide de deux évaporateurs atmosphériques qui servent à réchauffer le combustible. Reste ensuite à l’odoriser pour pouvoir l’acheminer jusqu’à la chaudière, où il alimente le brûleur. Si l’installation est autonome, grâce à la présence d’un automate chargé de gérer les vannes pneumatiques, nous assurons la télésurveillance de l’installation, les astreintes 24/24, les opérations de maintenance ainsi que le remplissage automatique de la cuve.

De quelles perspectives cette réalisation est-elle porteuse ?
T. B. : De nombreux acteurs étrangers opèrent en France dans le monde du gaz et du GNL, et il est clair que nous allons devoir faire notre place. Mais le jeu en vaut la chandelle : nous avons actuellement 150 clients alimentés au fioul lourd, qui vont devoir à leur tour changer d’énergie pour se conformer aux évolutions réglementaires, beaucoup plus contraignantes à partir de 2024-2025. Nous devons les accompagner dans cette transition et le GNL est un moyen adapté pour le faire. Voilà pourquoi nous avons l’ambition, dans la décennie à venir, de construire deux installations nouvelles chaque année. Sans oublier d’aller chercher les industriels déjà convertis au GNL pour leur proposer notre offre de fourniture, transport et maintenance.
P.-H. F. : Le projet mené à bien pour Knauf Industrie nous permet de faire reconnaître notre expertise technique dans la construction d’installations de regazéification. Aux yeux de nos clients industriels, nous sommes devenus un acteur légitime sur ce marché extrêmement compétitif et à marge réduite. La priorité est maintenant de poursuivre les efforts engagés avec la branche Gas Renewables & Power de Total pour améliorer la rentabilité de ce business.
Commentaires